Introduction to Mass Finishing Types of Finishing
What is a Mass Finishing?
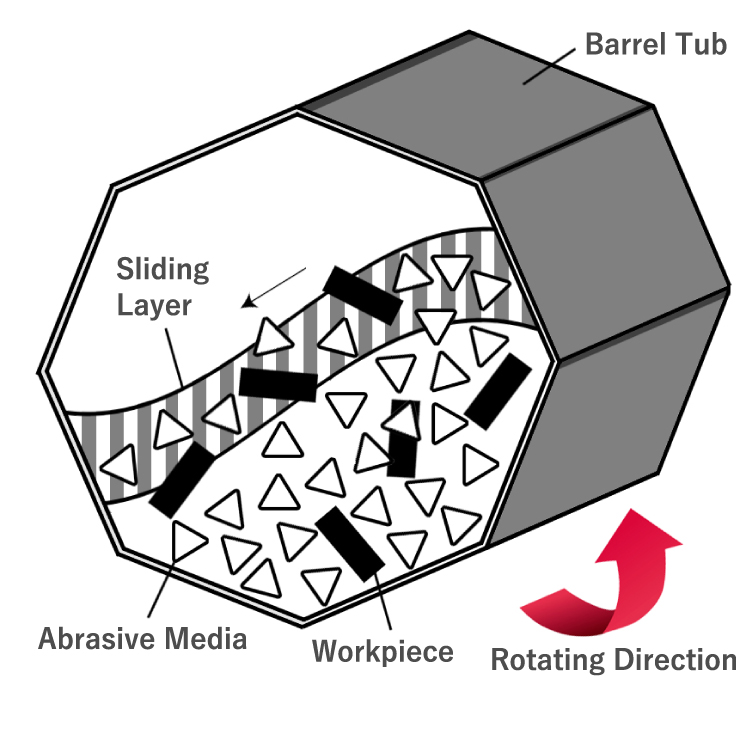
Abrasive media, work pieces, compound and water are loaded into barrels at a certain ratio and are put into motion lIke rotation or vibration. Abrasive media and work pieces rub each other caused by the difference in weight, shape, speed and direction of abrasive media and work pieces. The friction generated under such movement results in surface finishing.
Today, mass finishing process is widely employed throughout various industries such as automotive and electronic devices as the final manufacturing process.The finishing process includes deburring, smoothing, mirror finishing, radiusing and descaling.
3 Elements of Mass Finishing
Abrasive media, work pieces, compound and water are loaded into barrel tubs at a certain ratio and are put into motion. Abrasive media and work pieces rub each other caused by the difference in weight, shape, speed and direction of abrasive media and work pieces. The friction generated under such movement results in surface finishing.
Accordingly, mass finishing machines that operate barrel tubs, abrasive media for grinding workpieces and compounds for cleaning workpieces and abrasive media are called the "three basic elements of mass finishing," and a variety of purposes can be met by choosing each element appropriately.
3 Elements of Mass Finishing
Mass Finishing Machines
The barrel tub is rotated or made to vibrate by means of a motor and power transmission system.
Abrasive Media
Abrasive media is made up of abrasive grain that is held together mainly by a clay-based binder, and fulfills the role of grinding and polishing to finish workpieces while wearing itself .
Compound
Liquid or powder form whose main component is a surfactant contained in household detergents. It prevents lodging of abrasive media while cleaning the surface of workpieces at the same time.
Advantages of Mass Finishing
- Low processing cost
- Processing a large volume of work pieces at one time
- Nearly uniform finishing results
- Processing complicated work pieces
- No skill required
Finishing Method in Mass Finishing Periphery
-
Blasting
(Wet Blasting / Sand Blasting)This is the finishing method that removes burrs and scales by blasting abrasives from a nozzle with the force of compressed air to work pieces.
(in wet blasting, the blasting abrasive that contains water is like "slurry") -
Brushing
This finishing method rubs a work piece to a certain degree of depth with a wheel or cup type brush made of nylon, steel or brass filaments containing abrasives, and rotated at high speeds.
-
Belt Finishing
This finishing method rubs a work piece with an endless belt coated with abrasives
-
Center-less Buffing
This finishing method polishes a work piece by holding it between a cylindrical multi-layered buff rotating at high speed and an adjustment wheel for moving the work piece forward.By using the elasticity of the buff,it makes a small radius at the same time as polishing.
-
Shot Blasting
This is the finishing method to remove large burrs generated in a molding process by shooting fine metal granules (steel balls and grits) with the force of an impeller rotating at a high speed.
-
Electrolytic Polishing
This polishing method is used for dissolving burrs on workpieces. This is achieved by conducting electricity between a workpiece located on the plus side and an electrode on the minus side in electrolyte solution.
-
Magnetic Barrel (Magnetic Polishing)
The permanent magnets or solenoid coils are located under the spinner or around the barrel tub. Work pieces and magnetic media are loaded in the barrel. As the spinner rotates the magnetic field moves, which agitates the magnetic media to achieve the surface finishing.
-
Buffing
This polishing method is accomplished by rubbing work pieces with a rotating disc-shaped non-woven cloth or layered cotton cloth coated with abrasives.