Ceramic Inert Ball for oil refining and petrochemical industries
At petrochemical complexes, the raw material rude oil is refined to gradually be turned into gasoline, light oil, kerosene, and fuel oil, and other oil products. These processes involves an environmentally friendly desulfurization (the removal of sulfur in substances) process in which catalyst causes a catalytic reaction. Tipton's ceramic inert balls are used as filler that holds that catalyst.
Ordinary-press distillation and reaction basics
Chemical Reaction in a Reactor
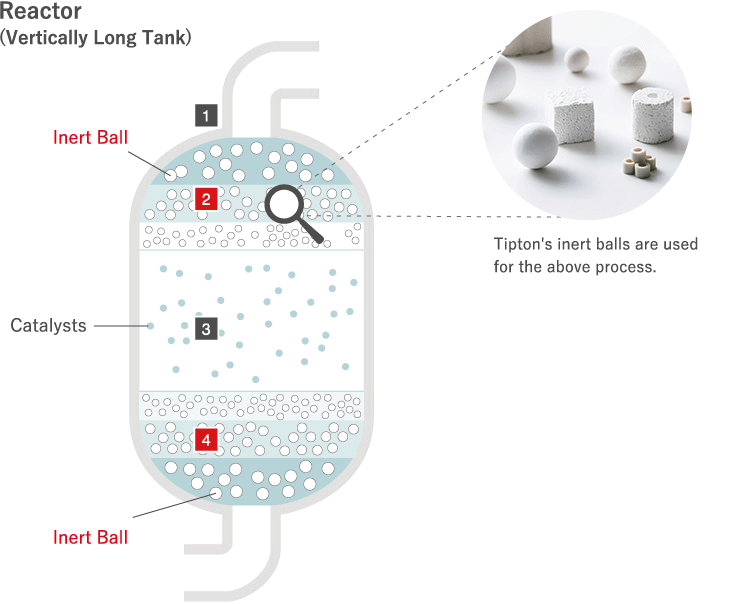
- The raw materials flow down from the upper part.
- The raw materials go through the inert balls, the catalyst area.
- The raw materials chemically react at the catalyst area and get chemically engineered.It becomes the secondary raw materials/products.
- The chemical engineered materials/products pass through the inert balls and flows to next process.
Heat Exchange Media for High Performance Industrial Furnaces (regeneration burner system, etc.)
The inside of the furnace, which is illustrated belowin center, is heated by the burner. This heating method has been innovated.
As exhaust & inhalation (of combustion air or/and exhaust gas) is passing through pipe left to right and left to right alternately, the alumina ball(illustrated middle left and middle right) is done heat exchange (heated & cooled).Asa result, this system contributes to fuel efficiency & CO2 reduction.
Regenerative Burner Mechanism
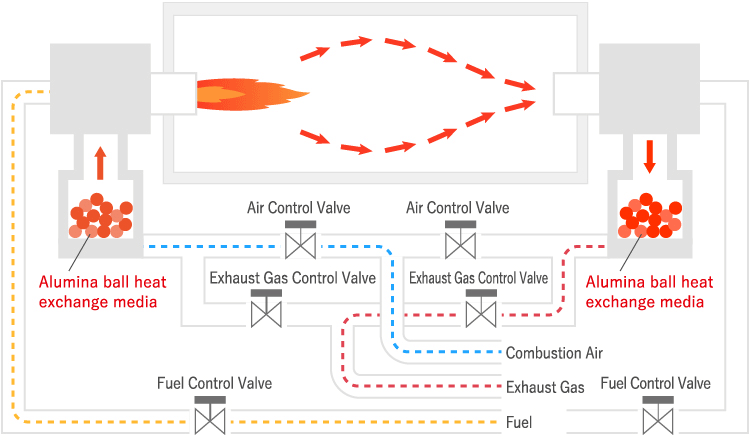
Our High Alumina Ball is also used as heat exchange media.
Heat Exchange Media ‘High Alumina Ball’ Cleaning System
Being exposed to a severe industrial environment (rapid quenching and heating), High Alumina Ball's surface is gradually stained by dust in the furnace causing decreased heat exchanging performance. In order to reverse the situation, Tipton's cleaning and polishing agents are used to enhance fuel efficiency and reducing CO2 emissions.